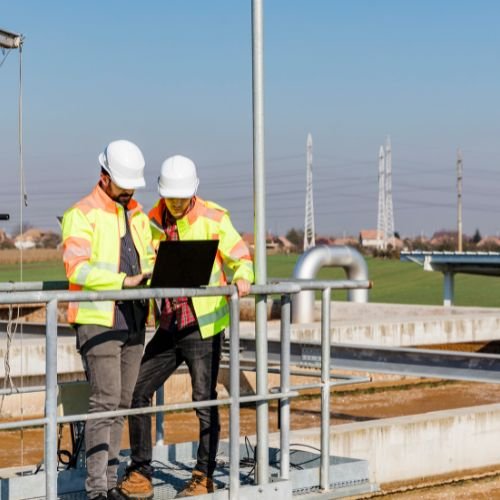
Water Treatment Plants
At Advance Control System (ACS), we engineer, manufacture, and implement highly customized and technologically advanced water treatment solutions. Our WTPs are tailored to meet the specific demands of each client, whether it’s a small community, a large industrial plant, or a municipal authority. With a strong focus on efficiency, reliability, and sustainability, our systems are designed to consistently produce high-quality water while minimizing energy consumption, operational costs, and environmental impact.
Water sources such as rivers, lakes, reservoirs, borewells, and even seawater often contain a wide range of contaminants. If not treated properly, these can pose serious risks to health, equipment, and the environment. Our WTPs are capable of addressing all major categories of impurities through a series of advanced and proven treatment processes.
Contaminants Treated in ACS Water Treatment Plants:
Suspended Solids & Turbidity
– Removal of visible particles, silt, and cloudiness in water
- Biological Contaminants – Elimination of disease-causing bacteria, viruses, protozoa, and algae
- Dissolved Organics & Inorganics – Reduction of naturally occurring and synthetic compounds
- Heavy Metals – Effective treatment of hazardous metals such as iron, lead, arsenic, mercury, etc.
- Chemical Pollutants & Dissolved Salts – Neutralization or filtration of unwanted chemicals from industrial waste or agricultural runoff
- Color, Taste & Odor – Aesthetic improvement to make water more appealing and usable
Key Features of ACS Water Treatment Plants:
- Multi-Stage Treatment Process – Each ACS WTP integrates a carefully designed sequence of processes—screening, coagulation, flocculation, sedimentation, filtration, and disinfection—to ensure complete and reliable removal of physical, chemical, and biological contaminants.
- Custom Engineered Systems – Every plant is uniquely designed to suit the specific raw water source and desired water quality output. We assess local water chemistry, usage patterns, and environmental factors before designing the plant.
- Advanced Filtration Technologies – Our WTPs utilize pressure sand filters, activated carbon filters, ultrafiltration (UF), or reverse osmosis (RO) systems depending on the end-use requirements, ensuring optimal clarity and purity.
- Smart Automation and Control – Equipped with PLC/SCADA-based automation systems, our plants offer real-time monitoring, remote diagnostics, data logging, and auto-controls for pumps, valves, and dosing systems—minimizing human error and downtime.
- Energy-Efficient Operation – We incorporate energy-saving pumps, motors, and process optimization algorithms to reduce power consumption and operational costs without compromising performance.
- Robust and Corrosion-Resistant Construction – Plants are built with high-grade stainless steel, FRP, or coated mild steel components, ensuring durability, long service life, and resistance to chemical and environmental corrosion.
- Low Footprint & Modular Design – Designed for compact spaces, our WTPs can be prefabricated or modular, allowing for easy installation, scalability, and relocation if required—ideal for both temporary and permanent setups.
- High Recovery Rates – Our systems are designed to maximize the usable output water and minimize waste, ensuring efficient utilization of water resources.
- Low Maintenance & Easy Operation – Simple-to-maintain systems with automatic backwash, easy access components, and self-cleaning filters reduce labor and maintenance frequency.
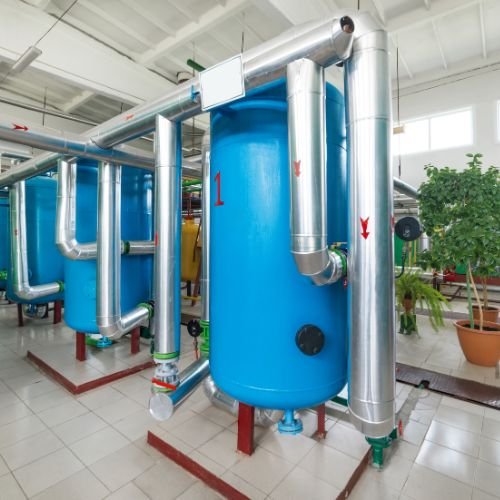
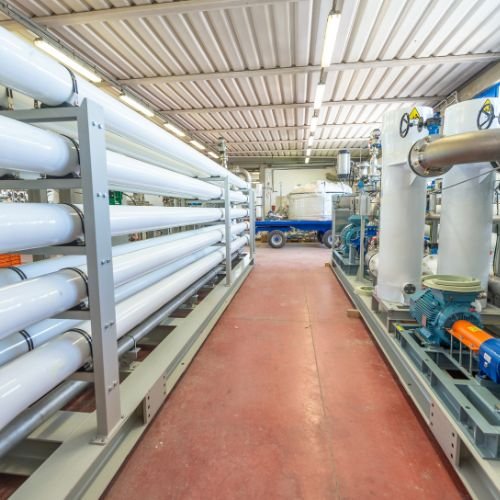
Key Processes Used in ACS WTPs
- Screening and Pre-Treatment – The initial stage of water treatment involves removing large debris and non-biodegradable solids such as leaves, plastics, rags, and grit. This is achieved through coarse screens and grit chambers, which protect downstream equipment from damage and blockages. Pre-treatment also stabilizes water quality before chemical treatment.
- Coagulation & Flocculation – Fine suspended particles in raw water (such as clay, silt, and organic matter) do not settle easily. Through coagulation, chemicals like alum or ferric chloride are added to destabilize these particles. In the flocculation stage, slow mixing encourages these particles to bind together into larger, heavier flocs that can settle out more easily. This improves the efficiency of sedimentation and filtration.
- Sedimentation – In this phase, water is directed into a sedimentation tank or clarifier. The heavy flocs formed during coagulation and flocculation gradually settle at the bottom under the influence of gravity. Clear water is collected from the top, while settled sludge is removed periodically from the bottom for further treatment or disposal.
- Filtration – To remove any remaining suspended solids and fine particles, the water passes through a series of filters such as Pressure Sand Filters (PSF), Activated Carbon Filters (ACF) and Multimedia Filters (MMF)
- Disinfection – This crucial step ensures the elimination of pathogenic microorganisms (bacteria, viruses, protozoa) from the water. Disinfection methods include ultraviolet (UV) Systems, chlorination and ozonation. The choice of method depends on application and client requirements.
- Advanced Treatments (if needed) – For specific water qualities or industrial applications, additional treatments may be included like Reverse Osmosis (RO), Ultrafiltration (UF), or Ion Exchange for high-purity or specialized applications.
- pH Correction and Conditioning – In the final step, the treated water is adjusted for optimal pH, taste, and safety. Chemicals like lime, soda ash, or carbon dioxide may be added to balance acidity or alkalinity. This ensures the water is non-corrosive and suitable for drinking or industrial use. Mineral dosing may also be applied to improve taste and health benefits (especially in potable water systems).